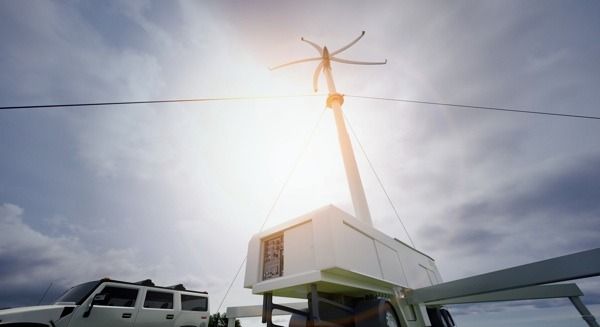
Design Methodology and Technical Attributes of the Uprise Energy 50 kW Portable Power Center
J
Jonathan Knight
Jonathan Knight
A study of constraints in the wind industry was conducted to guide the development process of the Uprise machine. The list is long, but here are the ones that effect energy capture are:
Uprise innovations have eliminated all of these constraints