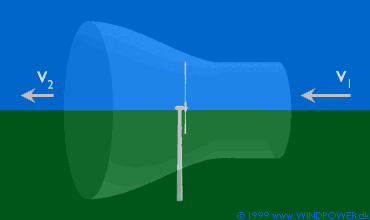
Problem In The Wind Industry and The Uprise Solution
Jonathan Knight
Jonathan Knight
The problems encountered in generating electricity from the wind and delivering the electricity to a user are numerous. This post will address the essential element of this industry, converting the kinetic energy in wind into electricity.
Other essential elements of conventional wind energy, which cannot be excluded, include:
We start with the premise that converting wind strength into electricity is our number one objective.
The formula to calculate the kinetic energy in steady wind is:
1/2AV3rho/1000 = kW
Once the Kinetic Energy (KE) of a steady wind has been calculated, there are various factors that reduce the captured energy to a NET OUTPUT.
Betz' Law says that you can only convert less than 16/27 (or 59.3%) of the kinetic energy in the wind to mechanical energy using a wind turbine.
KE at 100% of steady wind = 100%Betz limit = 59.3%Modern Rotor efficiency = 50%Transmission losses = -5%Transformer losses = -4%Inverter losses = -3%Reactive power losses = -15%NET POWER = 23%
The net energy from a Conventional Wind Machine (CWM) in a steady wind delivered to the user is approx 23% of the kinetic energy of the steady wind.
In most cases wind is not steady. Calculating the kinetic energy in a variable wind (wind gusts and lulls) is a function of amplitude and duration.
The calculation of the KE in a variable wind is not a function of the average wind speed due to the cube root power factor. KE above the average wind speed is greater than KE below the average wind speed.
A Conventional Wind Machine captures 23% of steady wind and none of the gust wind energy above the steady wind average. As a result, the real efficiency is 23/270, or 8.5%.
A Conventional Wind Machine does not seek nor capture gust energy.
The principle reasons why a Conventional Wind Machine does not seek or capture gust energy are EXCESS WIND LOAD and RPM CONTROL.
LOAD
When operating at near capacity, a wind gust may increase input power by 8 times, which overloads the machine.
The consequences of excess wind speed and power include:
A Conventional Wind Machine incorporates a variety of design elements to offset the excess power and wind speed.
Conventional Wind Machine nacelle fire caused by overloading
There are negative consequences resulting from the load and RPM constraints listed above.The rotor rpm of a CWM is constrained and remains relatively constant, regardless of the wind speed. As a result, Tip-Speed-Ratios (TSR) and blade efficiency are compromised.Energy is dumped to prevent overload and over revving.A fixed ratio step-up gearbox is used, which has inefficiencies, and is easily overloaded in wind gusts, which is the #1 industry failure.A transformer is required to stabilize the voltageAn inverter is used to stabilize the hertzAn induction generator is used which causes a lagging power factor and need for reactive power from the gridIn the event of a direct drive generator without the use of a gearbox, the low RPM of the generator causes cogging and flicker.Torque on the system is amplified when load is high and RPM is constrainedNoise from the blades is amplified when blade loading is highTeetering is amplified at high loads
In response to these constraints, Uprise has designed the PPC and the ECS to operate in a variable wind speed.
Ideally, a wind machine would optimize energy capture and deliver power as a ratio to the winds energy.
The Uprise machine has been designed to:
Uprise ECS driving the PPC
The above abstract summarizes the constraints of conventional wind machines, the additional Kinetic Energy in variable wind, and the methods that enable the Uprise machine to capture higher levels of energy.
In addition, due to its portability it solves two of the greatest constraints, transmission lines and/or reliance on fossil fuels.
Modern wind farms are located where wind currents are strong and steady to minimize the problems caused by wind variability. As a result, the power must be delivered to the user thru a transmission system, which is the #1 reason why 30% of the world’s population is not served with electricity.
The Uprise portable power center solves this problem.